Tank Linings
At MPC we offer professional tank lining services, specializing in a diverse range of storage tanks across Ohio and the entire USA. We are equipped to assist with a wide range of tank linings, for the following:
- Fuel, oil, petroleum storage tanks (AST’s)
- Water and wastewater treatment tanks: Digesters, Clarifiers, Containment Tanks and Canals, Denitrification Pools, Distribution Tanks
- Secondary containment tanks
- Silos
- Fertilizer tanks
- Food & Beverage storage tanks
- Pharmaceutical tanks
- FRAC tanks
- Acid storage tanks
- Chemical storage tanks
- And many more
We specialize in cost-effective, reliable tank linings, whether new or for relining existing ones. Our expertise in material selection and precise application minimizes the risks and expenses associated with lining failures.
Partner with us, a trusted industry leader, for tailored solutions and peace of mind in safeguarding your investment.
Send Your Request And Get A Free Quote





















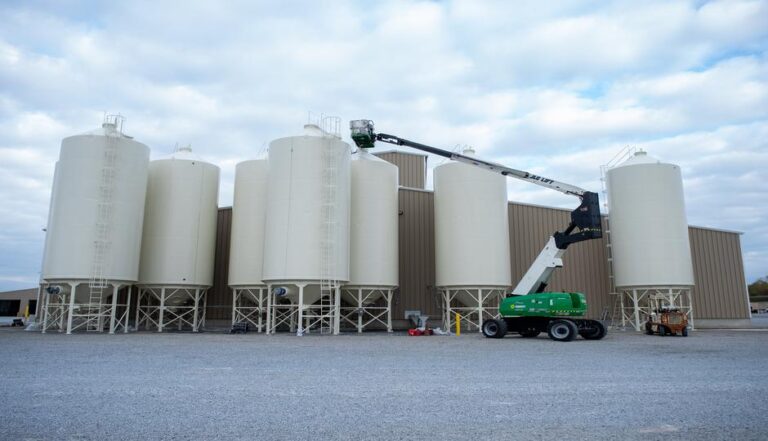
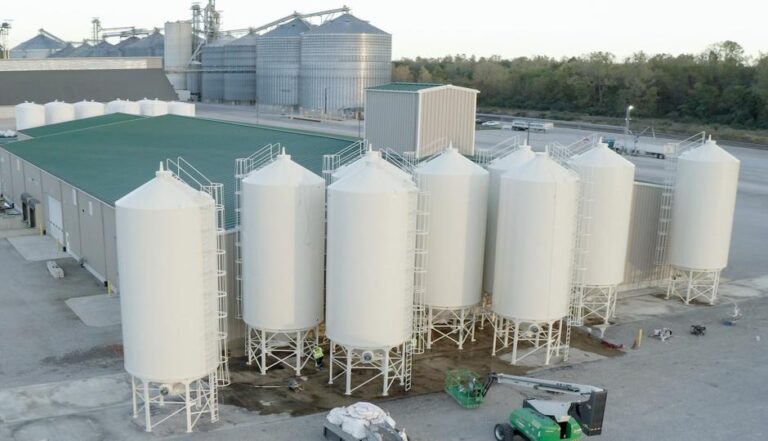
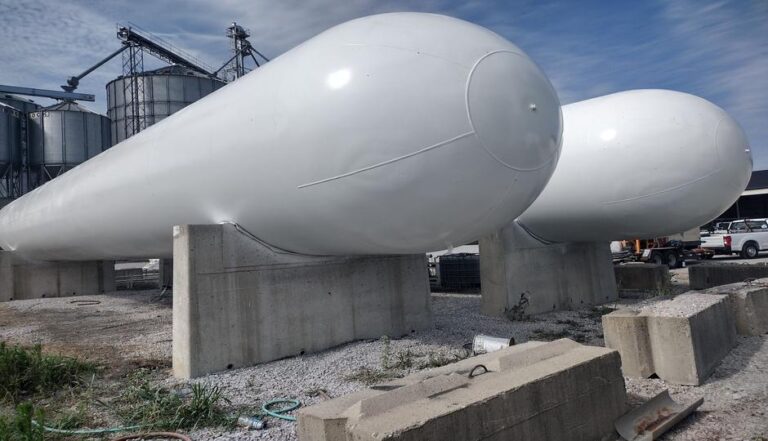
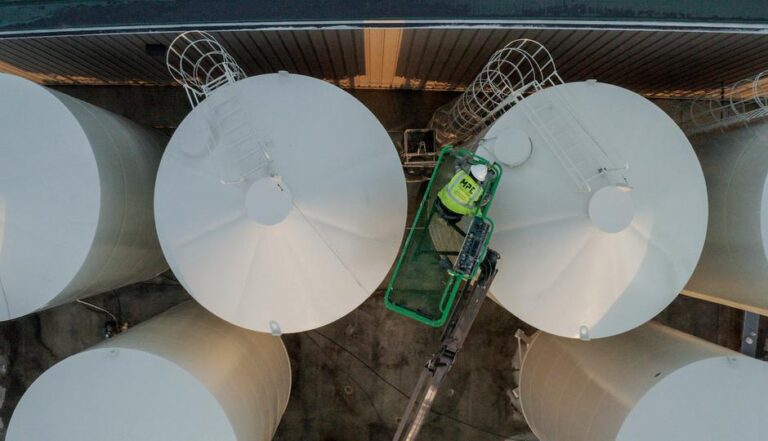
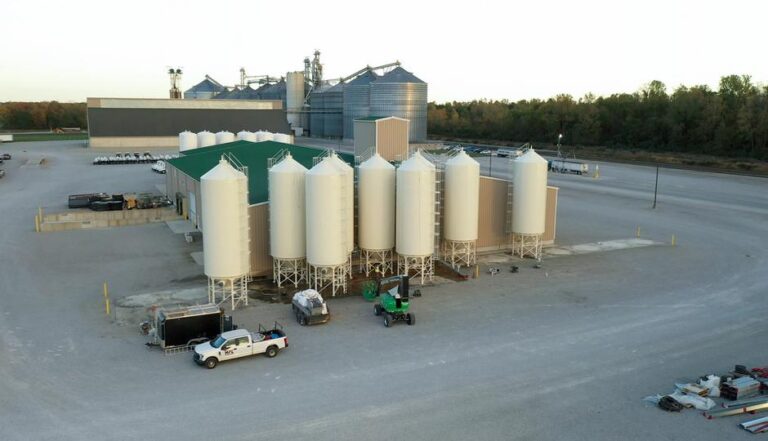
Why Choose Us?
Nationwide Tank Painting
Over 5000 Tanks Restored
Preferred Contractor
Accident Free Safety Record
Best-In-Class Warranties
Zero Downtime Process
100% Eco-Friendly
Anywhere In The USA
Benefits of Tank Linings
Product Protection
Asset Protection
Avoid Costly Emergency Downtime
Tank Lining Options We Provide
Vinyl Esters
Single coats of vinyl ester tank linings are offered in a range of six to 40 mils. Vinyl ester linings excel in high-corrosion service, including acid resistance and high-temperature applications. Options for abrasion-resistant and Low Surface Energy (LSE) coatings are also available.
Zinc Silicates
Zinc Silicate Tank Linings provide excellent protection for alcohols, solvents, and potable water. Zinc silicate tank linings can withstand almost all chemicals between pH 5.5 and pH 10. Zinc tank linings are also typically applied in a single coat, which can lead to less downtime and be more economical to apply.
Glass-Mat Reinforced Linings
Without regular maintenance, corrosion can literally eat away at your assets, leaving you prone to costly structural repairs and, even more significantly, to costly downtime. Regular preventative corrosion maintenance, such as painting, can preserve your assets for decades to come.
Epoxies
Epoxy tank linings offer the widest chemical resistance and one of the better temperature resistances among tank lining options. Depending on the specific type of epoxy used, these linings can handle products ranging from pH 3 to pH 14. They are typically used for storing biofuels, petroleum products, water, alkaline solutions, vegetable, and mineral oils. Another advantage of using an epoxy lining system is its greater flexibility in changing the product stored in your tank, as it's less porous compared to other linings. This reduced porosity makes it easier to clean, allowing you to change the product in the tank with a lower risk of cross-contamination.
Polyurea
Polyurea, a spray-applied, plural-component system, cures in just 6-8 seconds and is typically applied at 60-120 mils. This seamless, chemically bonded lining offers superior flexibility, with over 2,000 psi tensile strength and 300% elongation, making it ideal for environments with frequent temperature fluctuations. Unlike epoxy and hard thin film coatings that are prone to cracking, Polyurea adapts to expansion and contraction without damage, ensuring longevity. Its quick curing time and robust strength also enable it to repair tank holes effectively as part of a multi-layer lining solution.
Selecting the Ideal Tank Linings for Your Needs
At Markleys Precision Company, we prioritize understanding your specific requirements to ensure we choose the optimal tank lining solution for you. Here are the key factors we consider:
- Chemical Composition: What will be stored in the tank? Knowing the chemical makeup of the product is crucial for selecting a compatible lining.
- Temperature Management: What temperature will the tank maintain? Different linings perform variably across temperature ranges.
- pH Level: Understanding the pH level of the stored product helps us determine the lining’s chemical resistance needs.
- Usage Frequency: How often will the tank’s contents be changed or used? This affects the durability requirements of the lining.
- Tank Size and Capacity: Knowing the dimensions and desired capacity of your tank ensures we provide a lining that maximizes storage efficiency.
- Environmental Conditions: We assess the ambient environment, as extreme or fluctuating temperatures can impact the lining’s performance, leading to expansion, contraction, and potential cracking.
- Downtime and Installation Speed: We understand that time is money. The cost of downtime and the speed of lining installation are key considerations in our decision-making process.
Choosing the wrong lining can lead to severe consequences, such as in the case of Jet A-1 fuel storage, where non-compliance with strict safety regulations can render the fuel unsellable. Trust us to provide a tailored lining solution that ensures safety, efficiency, and regulatory compliance.
Essential Steps for Optimal Tank Lining Performance
It may seem obvious, but the tank must be completely emptied of product and gas to ensure safety during the application. This includes ensuring that the atmosphere in the tank is breathable, as CO2 and other noxious gasses can quickly build to lethal concentrations in the confined space of a tank. Having good, actionable safety plans for emptying the tank and ventilating it properly is crucial for the safety of personnel entering the tank.
Choosing a quality liner that meets the specifications for properly storing your product(s) is as important as the surface preparation and application of the liner itself. For tank interior liners, we follow the industry standard, which is to abrasive blast to an SSPC SP10 near-white blast spec at a minimum, ideally with a clean, low-dust garnet blasting abrasive for a cleaner finish and to avoid impregnation of media in steel, as can happen with coal slag blasting media or similar.
Once properly blasted, removing the debris and dust from sandblasting is critical before application. Using a clean, dry, oil-free air source is very important while blasting to maintain a clean substrate (carbon steel tank).
Our experienced applicators or contractors who apply the coating, are familiar with the product and the ambient conditions (temperature, relative humidity, dew point, etc.) on the job site, they know the proper cure time to return the tank to service, which is also critical.
We understand that every second counts during any shutdown, whether planned or unplanned, so it’s critical for us to get your tanks back into service as quickly as possible.
The challenge with many coatings is that drying time can be up to three days before a second coat can be safely applied. If your downtime for tank lining is costing tens of millions a day, each additional day saved is crucial. Wet-on-wet application or a polyurea coating could be great options to help speed up the liner installation process.
If you need help with any tank lining needs or have questions about our process, don’t hesitate to give us a call. Our knowledgeable staff would be happy to assist with this critical process.